Researchers at the Commonwealth Science and Industrial Research Organization (CSIRO), Australia’s national research agency, deployed quantum machine learning to fabricate semiconductors of the future.
The researchers showed that their approach outperformed classic AI computing currently used in semiconductor design and fabrication and could change how microchips are designed.
Semiconductor design is where experts from areas such as electrical engineering, material science, and computing get together to build integrated circuits that power modern electronic devices. Expertise from diverse fields is put in, then rigorously tested to determine if the device can meet the performance criteria set for the device.
In the age of high-performance computing and artificial intelligence (AI), semiconductor design is also being improved with these tools. Classical machine learning (CML) has been deployed in these areas before.
However, its performance degrades in small-sample non-linear scenarios. This is why researchers at CSIRO were keen to explore if quantum machine learning (QML) could be used instead.
Critical semiconductors but notoriously difficult
The research team, led by Muhammad Usman, a professor and head of quantum systems at CSIRO, focused on modelling the Ohmic contact resistance of the semiconductor material in their work. This is the measure of the electrical resistance where the semiconductor comes in contact with the metal, and current can flow easily.
While this is critical in semiconductor design, it is also the most difficult to model. The research team used their quantum machine learning approach on data from 159 experimental samples of GaN HEMT (gallium nitride high electron mobility transistor). These semiconductors offer better performance characteristics than silicon-based semiconductors.
The researchers first used a broad range of parameters but then narrowed them down to determine which factors influence the fabrication process. Initially, the list was reduced to 37 parameters for each experiment and then to five for a principal component analysis.
“The quantum computers that we currently have have very limited capabilities,’ explained Usman to Cosmos. “So we wanted to simplify it. We wanted to make sure that we can reduce the problem’s dimensionality intelligently and do it within the capabilities of the current quantum processes.”
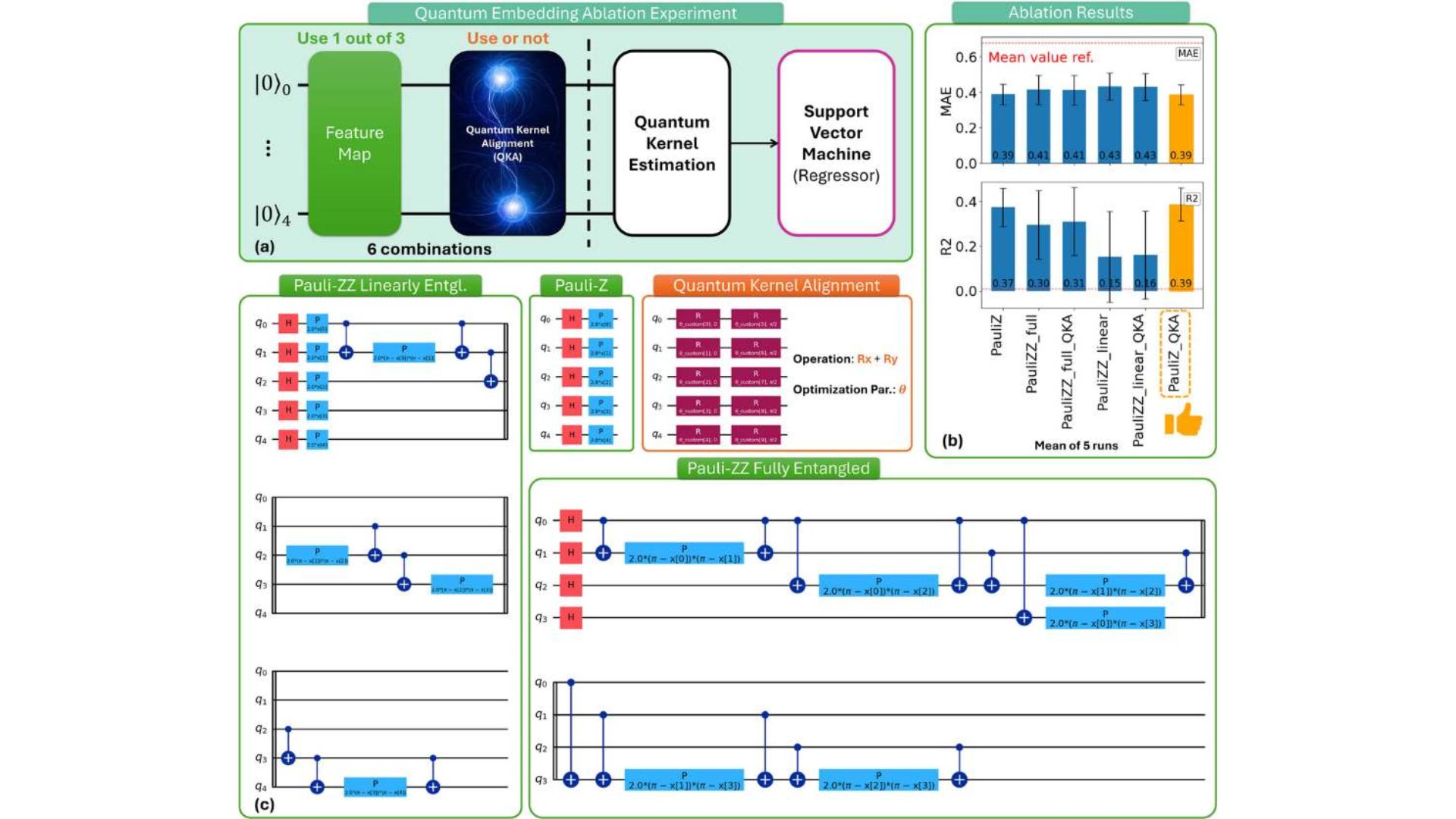
Working the quantum magic
The researchers developed a Quantum Kernel-Aligned Regressor (QKAR) architecture to work on the quantum component. The QKAR converts classical data into quantum data in five qubits.
This mapping to qubits is critical to begin the machine learning process, which occurs through a quantum kernel alignment layer. This layer extracts the important features from the data sets, and a classic algorithm is then used to retrieve the information.
“This classical machine learning technique takes that outcome that the quantum method has extracted, and then it’s trained to guide back to the fabrication,” added Usman.
“It can tell us the important parameters in the fabrication process, which play the critical role, and what needs to be changed or tuned to optimise fabrication.”
The QKAR approach outperformed seven different CML algorithms that have been developed to work on this problem. More importantly, since the method requires only five qubits, it can be deployed to solve fabrication industry problems immediately.
“Our results show that quantum models, when carefully designed, can capture patterns that classical models may miss, especially in high-dimensional, small-data regimes,” said Zeheng Wang, a quantum researcher at CSIRO, who was involved in the work.
“We validated the model by fabricating new GaN devices, which showed optimised performance, and, through quantum kernel spectrum analysis, confirmed QML’s ability to generalise beyond training data.”