-
By Wu Po-hsuan
and Jake Chung / Staff reporter, with staff writer
The National Institutes of Applied Research’s National Center for Instrumentation Research has said that it has developed technology to help the semiconductor industry address the issue of increased scrap rates for semiconductor wafers resulting from the use of silicon carbide.
Institute researcher Lin Yu-hsuan (林宇軒) said semiconductors are being increasingly used in electronic vehicles, artificial intelligence hardware and green energy-related industries.
Such industries demand semiconductors that are functional in high-pressure, high-temperature and high-frequency environments, which require wafers to be made from silicon carbide, also known as carborundum.
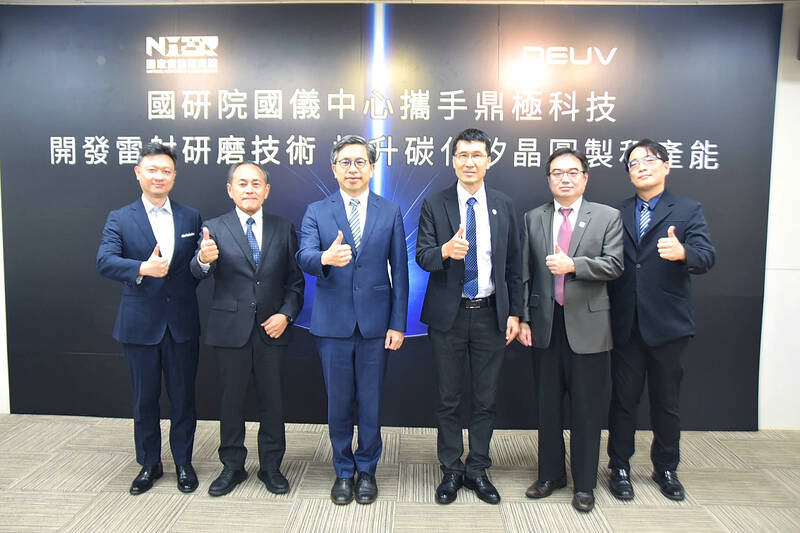
Photo: Wu Po-hsuan, Taipei Times
Silicon carbide has a 9.2 rating on the Mohs scale — which is used to determine the scratch resistance of minerals — second only to diamond, which has a rating of 10, the institutes’ president Tsai Hung-yin (蔡宏營) said.
Silicon, which is commonly used in semiconductor production, has a rating of 7, meaning that silicon carbide is three times harder, Tsai said.
Damages to cutting tools used in processing silicon carbide increase expenses, while cutting takes six to 10 times longer than silicon, and grinding takes three to five times longer and costs more, he said.
Wafer scrap rates have reached up to 5 to 10 percent, a rate that is hard to bear for manufacturers when the price for a wafer is NT$300,000, he said.
The institute uses a nanosecond pulsed laser hitting wafers 100,000 times per second, and the heat softens the silicon carbide exterior until hardness reaches 2 percent of the original, he said.
While the use of picosecond and femtosecond laser technologies can obtain the same results, they cost more, Lin said.
Nanosecond pulse lasers allow the manufacturing productivity to increase by 30 percent, and reduce overhead per wafer from US$23.3 per wafer to one cent, as well as reducing scrap rates to lower than 1 percent, Tsai said.
The center has given exclusive authorization to Deuvtek Co to trial mass production, he added.
The maturation of the technology would enable Taiwanese companies to process other hard materials such as gallium nitride, ceramic substrates or other advanced semiconductor packaging materials, he said.
One can only see the practical challenges faced by the industry firsthand at the factory, Deuvtek president Shoichi Sakanishi said.
Laser-grinding technology helps reduce material waste and virtually eliminates stress during operations, Deuvtek CEO Chyan Jiunn-yih (錢俊逸) said.