The push by many American manufacturers to “onshore” and “reshore” production in the United States has taken hold in a major way at X-FAB Texas in Lubbock, Texas. The company and its nearly 500 workers are manufacturing microchips practically around the clock in the Hub City of West Texas, employing the latest silicon-carbide technology and filling orders as quickly as possible from automotive suppliers and other customers that are thrilled to have a reliable domestic source for such crucial state-of-the-art components.
“Now, many companies want production of components in the global region they’re in,” said Lloyd Whetzel, the retiring CEO of X-FAB Texas. “The big driver for our automotive customers was the chip shortage they experienced over the past few years because of the supply chain [disruption] getting chips from Taiwan and elsewhere. They want to back off from globalization and emphasize domestic supplies, to protect and access what they need. It’s a big mindset change by the industry.”
Plus, the U.S. government has been promoting domestication of manufacturing through a new industrial policy formulated by the Biden administration that provides hundreds of billions of dollars in grants, loans and other financial incentives to companies, foreign or domestic, who site chip factories in our country.
X-FAB has been ahead of the game and hasn’t required any nudge from the federal government. Its plant dates from the heyday of U.S. microchip manufacturing 45 years ago, but the company’s latest boom results from a new strategy X-FAB pursued beginning just a decade ago: to bet on silicon carbide for the next generation of chips for U.S.-made automobiles and other devices.
That was long before the intense electrification of the automotive fleet made automakers even thirstier for X-FAB’s silicon-carbide technology. X-FAB’s new chips are helping automakers push the envelope on the crucial aspect of electric-car range, potentially to as far as 1,000 miles, which would put all-electric vehicles in a league of their own in terms of how far they could carry passengers before needing more fuel.
“It’s still an emerging phenomenon,” Whetzel explains. “Silicon carbide is a more efficient substrate than silicon, which has dominated chips for 60 years. And it operates at higher temperatures as well as at a higher frequency than silicon, which also adds to its efficiency. It’s a rough estimate, but if you convert power management in an electrified vehicle from silicon to silicon-carbide chips, the car can go about 10 percent further just by making that change in power management.
“You can also make batteries last longer because less energy is lost; if you can turn something on and off faster, you waste less energy,” he adds. “In turn, all of that reduces the weight of the modules and systems that automakers use because conductors, capacitors and other things associated with the rest of the module become smaller.”
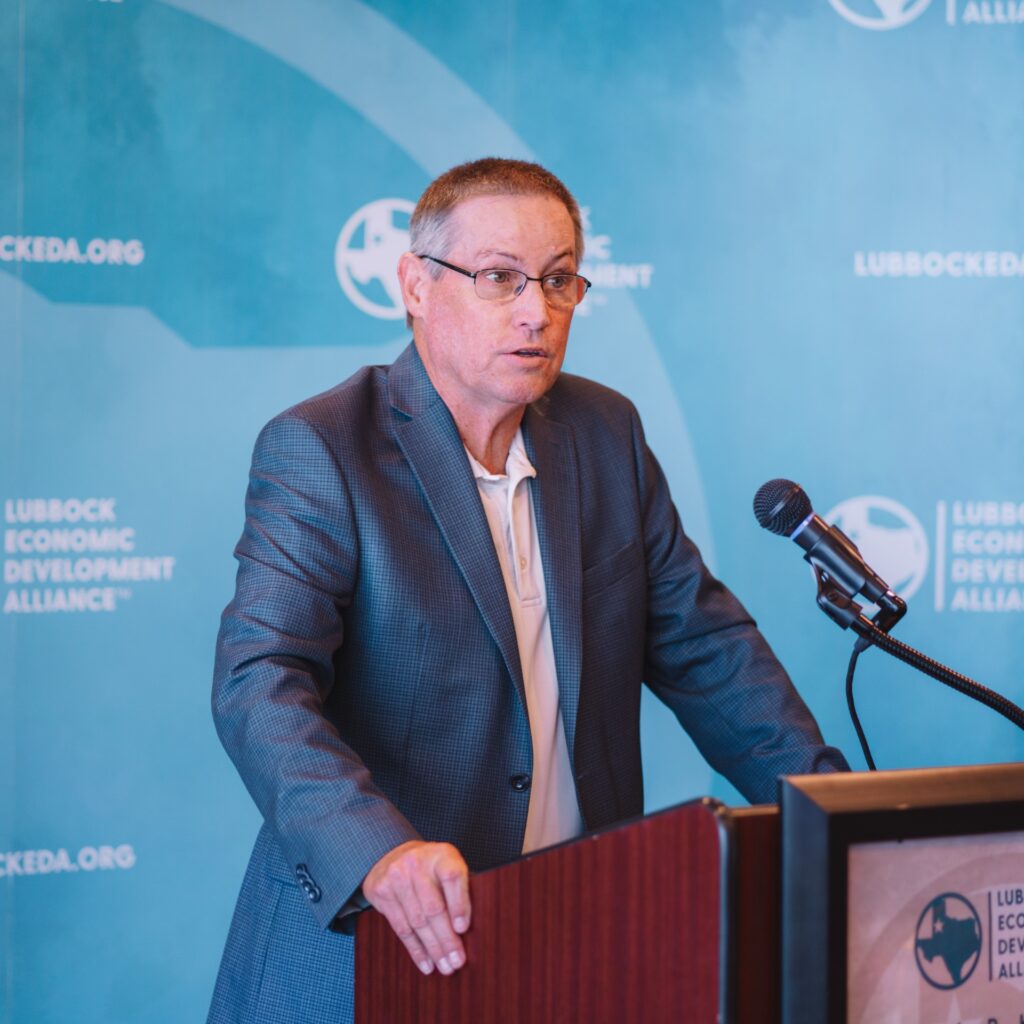
production of components in
the global region they’re in.
They want to back off from
globalization and emphasize
domestic supplies, to protect
and access what they need.”
—Lloyd Whetzel, X-FAB Texas
Given the advantages of silicon carbide, other sectors are picking up on X-FAB’s potential. “Data centers are another area that is catching on,” Whetzel says. “Companies just keep building them because with smartphones, people just keep adding data, doing viral videos and so on, and it takes data centers to create and maintain a cloud large enough to handle all of that. In infrared satellite views, you can see them just glowing at night all around the world because of all the power they use and heat they generate.”
X-FAB is growing its silicon carbide (SiC) business, partly because it is the only pure-play foundry in the U.S. manufacturing on six-inch wafers and will be positioned to manufacture on eight-inch wafers when the decision makes proper business sense. “Theoretically, we can run the same number of six-inch wafers on our line as four-inch wafers with the same amount of work, because there’s not much more material involved,” says Whetzel. “We get that economy of scale so it’s less cost per device, and that’s what customers are looking for to compete in a global market.”
Besides the security of domestic supplies for important manufacturing customers, X-FAB’s growing silicon-carbide business is also providing a significant sustainability boost compared with traditional silicon-chip output. PowerAmerica, a U.S. Energy Department initiative established in 2014 to promote domestic chip making, estimated that if the power management of all the data centers were switched to silicon carbide from silicon, it would save enough energy that the world’s largest nuclear reactor could be turned off.
An operating unit of a Belgium-based holding company, X-FAB Group, X-FAB Texas relies on Lubbock’s technology and education resources to keep growing into its customers’ expanding needs. The city’s South Plains College recently opened a technical training center for various technologies, and “most of our engineering talent” comes from Texas Tech University, Whetzel says.
“We’ve actually hired a number of people who went to Texas Tech and then left to work somewhere else, but they decided to come back to this location with their experience in industry,” he says. “We’re putting it to good use.”