Many people worldwide have used modern phones, solar panels, televisions, PC gaming, and other electrical products that rely on powerful microchip functions. While it is impossible to imagine how life would be without the tiny chips, many have no idea how these products are made. These chips use a process known as semiconductor manufacturing, specifically a process known as wafer processing. This article will discuss more details about this process.
Why Use a Silicon Wafer?
A common question some people ask when they learn that the process of making this chip uses silicon is: what is the reason behind it? Silicon is certainly not the highest-performing, energy-efficient material and does not deliver the most processing power, yet it is the most commonly used. This chip element has the right combination of factors that make it better suited for mass production. The production of these chips starts with the silicon wafer, a thin slice of highly pure silicon wafer. It is produced through a process known as wafer processing. These wafers create the ideal location for intricate electronic components that work together to serve the purpose.
Disposition Process

One thing that many need to know is that the creation of the chip involves various processes so that it can transform into a functional microchip used in various electronics. The first step that manufacturers have to take is deposition. The process involves cutting the silicon from a salami-shaped bar and polishing it to extreme smoothness. During the process, the films of conducting and isolating are deposited into the wafer. The wafer gets semiconducting materials to increase the precision. The disposition process is a crucial step in manufacturing the chips. This is because the products get the materials needed to achieve a specific property or function at this stage.
The Sizing
It is prudent to understand that not all the wafers in electronic products are created equally in size and composition. While some wafers have thousands of chips attached to them, some can have as few as a dozen. This is because the wafers of various products come in different sizes, which means they accommodate multiple chips. Therefore, during wafer processing the manufacturing process of these products, manufacturers have to cut down the length to fit the wafer. This process is known as lithography. It primarily uses diamond cutting tools to cut. After the cut, the wafer is exposed to ultraviolet light to give it a light-sensitive coating known as photoresists.
Designing
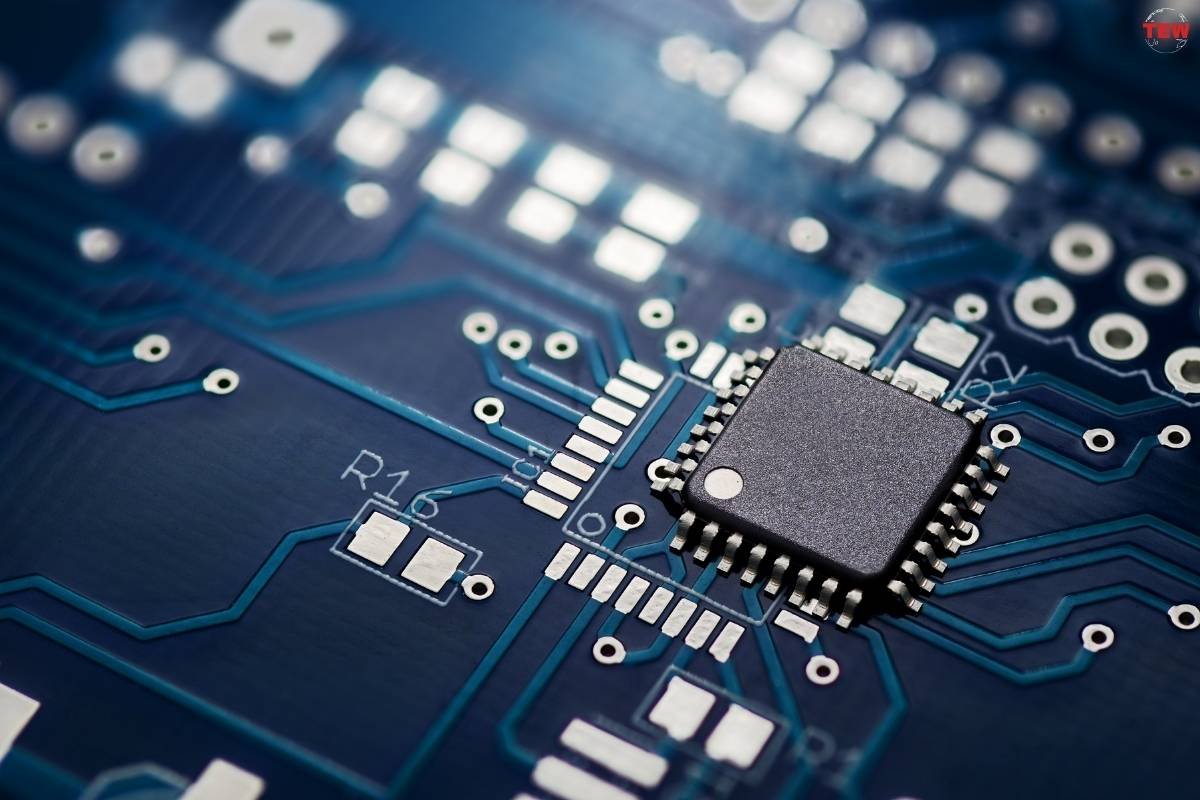
Each company or device has a unique design for the wafer. Getting the product to this design is known as the etch process. This is where the manufacturing companies design and shape the wafer into the desired pattern. However, this is a sensitive process, which is why manufacturing companies take the time to ensure that they do not cause any damage to the underlying layers of the structure. This is primarily important when cutting a wafer that has thousands of layers. Note that any slight damage to the chip means the wafer is unsuitable for use.
Ion Implementation in wafer processing
Implementing ion is another vital step in wafer processing. This involved installing the positive or negative ions into the products. The type of ion the product gets depends on the conduction properties. This step is critical because the silicon that creates these chips is not a perfect conductor or insulator. Therefore, companies install the ions into the silicon crystal to allow easy flow of electricity in a process known as ion implementation through controlled electrical conductivity.
Wafer manufacturing is the cornerstone of semiconductors. It enables manufacturers to produce intricate microchips that power the digital world. Therefore, those looking for insight into this incredible technology now understand and appreciate the important phases of creating these chips.