Although semiconductor manufacturing is absolutely vital in the field of innovative technology, the process of creating these materials is not always kind to the planet. One estimate suggests that the fabrication of semiconductor circuits on a 150-mm wafer consumes approximately 285 kWh of power, equating to 1.6 kWh per square centimeter. This activity is responsible for contributing to 31% of global greenhouse gas emissions, surpassing the emissions from electricity generation, which account for 27%.
That is exactly why the industry depends upon future-forward professionals like Dimitri Margolin, whose dedication to environmental sustainability has driven major progress in this arena within the semiconductor manufacturing industry.
A Key Industry
“We need these materials – they define modern life,” says Margolin. “But our industry faces some major environmental challenges, like substantial chemical usage, waste generation, and energy consumption.”
Margolin’s pioneering work addresses these challenges head-on, demonstrating a profound commitment to integrating sustainability into the core of semiconductor fabrication processes.
“There’s no one easy answer to achieving sustainability in semiconductor fabrication,” he explains. “I’ve long been a proponent of a multifaceted approach – targeting key environmental concerns through innovative projects and initiatives.”
But he doesn’t just talk about change. He’s making it happen. Margolin’s efforts to reduce chemical usage, minimize waste, and implement energy-efficient methodologies demand new standards for eco-friendly manufacturing that align closely with broader global sustainability goals.
Reducing Chemical Usage
Margolin has directed notable efforts toward an endeavor to reduce the reliance on hazardous chemicals in the CMP (Chemical Mechanical Planarization) process, a critical step in semiconductor manufacturing.
“The conventional CMP process involves the use of abrasive slurries and cleaning solutions, which can be detrimental to the environment,” Margolin explains. That’s why he spearheaded the development and adoption of eco-friendly slurry formulations that maintain the high standards required for wafer planarization while significantly reducing the toxicological profile of the chemicals involved.
In crafting this initiative, Margolin has to call upon his thorough understanding of chemical properties and their interactions with semiconductor materials. This rare skill set allowed him to pursue extensive research and development that involved collaboration with chemists, environmental scientists, and industry partners to identify alternative compounds that offer the same, if not better, performance as traditional slurries without the associated environmental risks. This work has resulted in a notable reduction in hazardous chemical usage, contributing to safer manufacturing environments and lessening the industry’s ecological footprint.
Minimizing Waste
Margolin has also contributed significantly toward waste minimization. Semiconductor fabrication is traditionally associated with high levels of material wastage, from excess silicon from wafer production to spent chemicals and water from cleaning processes. To counter this, Margolin has conceived of new solutions in process optimization that have dramatically reduced waste output.
First, he has implemented advanced monitoring and control technologies, which allows the CMP process to use materials more efficiently – thus decreasing the amount of waste generated. Also, Margolin has championed recycling and reuse initiatives within the fabrication process. He has been instrumental in developing systems that treat and recycle water used in the CMP process, reducing the demand for fresh water and minimizing wastewater discharge.
Energy-Efficient Methodologies
Energy consumption is another critical concern in semiconductor manufacturing, with fabrication facilities operating around the clock and consuming vast amounts of electricity. Margolin’s work in this area focuses on enhancing energy efficiency throughout the semiconductor production process. He has introduced cutting-edge energy management systems designed to optimize power use, which has reduced the energy footprint of semiconductor fabrication operations.
Margolin has also been lauded for his use of smart tech into manufacturing equipment. He utilizes technologies that enable real-time energy consumption monitoring and automatic adjustments to minimize power usage without compromising process quality or throughput. Margolin has also advocated for the use of renewable energy sources in semiconductor manufacturing facilities to further align his work with global efforts to combat climate change.
Global Sustainability Goals
Margolin’s contributions to environmental sustainability in semiconductor manufacturing reflect his deep devotion to preserving our precious planet. He pushes for global sustainability goals that are specifically related to responsible consumption and production (Sustainable Development Goal 12) and climate action (Sustainable Development Goal 13).
His work has been able to reduce chemical usage, minimize waste, and implement a new wave of energy-efficient methodologies. Margolin is dedicated to advancing the semiconductor industry’s environmental performance and to contributing to broader efforts for a sustainable future.
Dimitri Margolin is a pioneer. He isn’t afraid to test the boundaries of what’s possible in order to go green while getting the job done. His creative projects show how technological innovation can be harnessed to achieve environmental objectives. It’s clear to see why Margolin is so respected in his field – he’s a shining example of how to improve processes while also making manufacturing better for the planet.
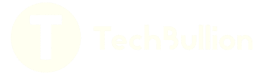
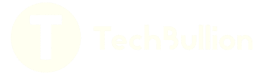