Semiconductor talent shortage in India: How to make 85,000 jobs in semiconductors a reality
As much as the size of a chip in a wafer fab substrate, is the availability of talent for semiconductor design and manufacture. That’s a bit of a stretch, yet the on-ground reality is the challenge of a wafer-thin resource pool. Something must be done soon, lest India becomes a dot on the global semiconductor map.
While inaugurating ‘SEMICON India 2024, Prime Minister Narendra Modi said: “Today’s India inspires confidence in the world. Our semiconductor sector is on the brink of a revolution, with breakthrough advancements set to transform the industry. Our dream is that every device in the world will have an Indian-made chip.”
Let’s check industry projections, skillsets required, and steps taken by the government and private sector to build and design fabrication facilities, increase capability in assembly, test and packaging, and nurture new talent.
As a preamble, here is an extract from a report by Boston Consulting Group, USA, on the urgent need for workforce development: “As semiconductor companies pursue ambitious development plans in the context of a tight labour market, they rely on access to engineers and technicians to fill both high and mid-skill positions. Improving workforce development across established and emerging regions, while advancing immigration policies to foster global talent flows, will be vital to the semiconductor industry’s future resilience.”
Extending the preamble, and prior to examining steps taken to build resilience in the semiconductor supply chain, let us understand the significance of semiconductors, whether it is early days yet, and which countries dominate the vertical.
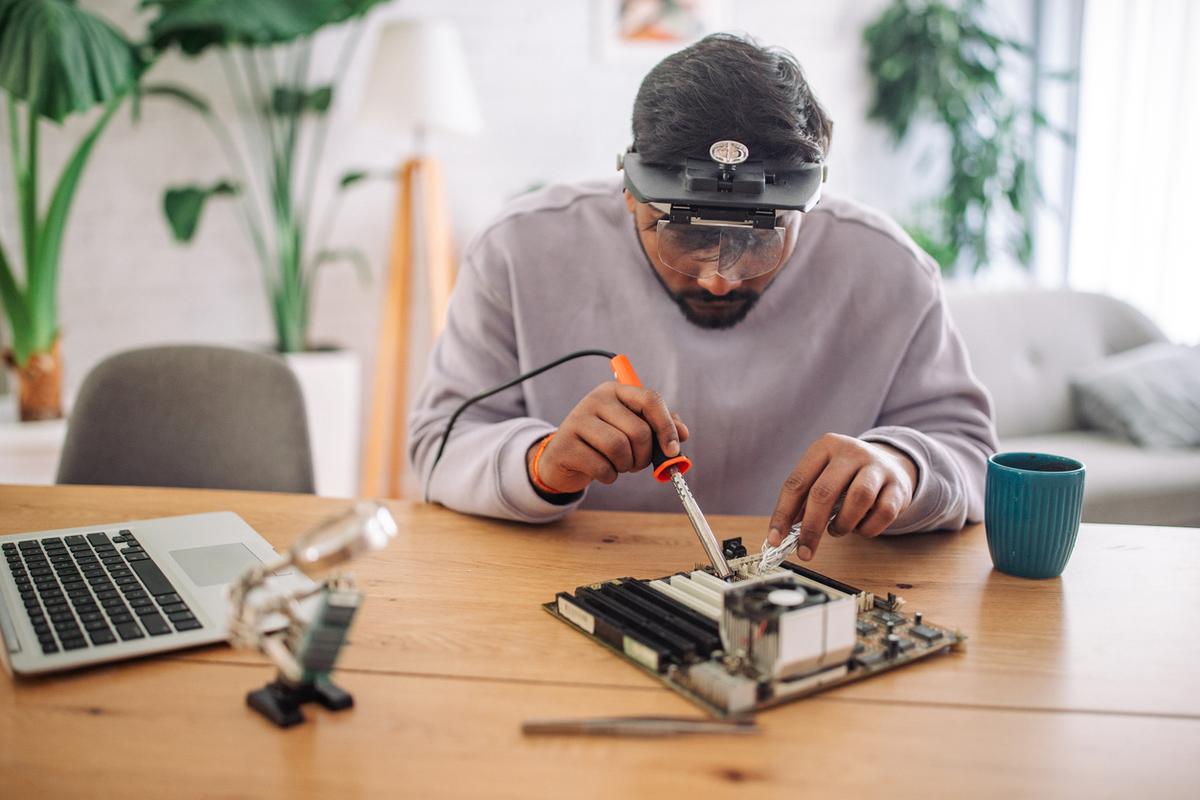
To create a strong semiconductor industry, the supply side of critical minerals such as rare earths must be stabilized and dependence on imports reduced significantly. | iStock/Getty Images
Semiconductors 101
Though we may not know it, we benefit immensely from the invention in our daily lives. Our smartphone, digital camera, television, washing machine, oven, refrigerator, and LED have semiconductors in some form. Or take ATMs, trains, the internet, and most communication channels – they rely on such materials to perform better, for longer.
In healthcare, semiconductors play a role in filling prescriptions, monitoring neonatal patients and in labwork that deals with transferring and storing diagnostics results. Logistics systems, shipping of consumer goods and perishables use semiconductors to save energy. In the defence domain, they enable development of advanced radar systems, communication devices, navigation systems, and weaponry.
In electric vehicles, which India is turning to for sustainability and green energy, semiconductors are a sine qua non to power the in-built Advanced Driving Assistance Systems which enable parking assistance, collision warnings, autonomous emergency braking, and other advanced features that make EVs safer and easier to drive, or drive without a driver.
To understand the role of a microchip within a semi-conductor, consider two use cases:
1) An EV is accelerating to a high speed. The driver must slow down suddenly, requiring the current to travel in reverse.
2) A tourist views a digital map of a country, zooms in on a large city, locates a lone street, and then wishes to return to the first frame.
In both instances, the chip is a semi or partial conductor that transmits and manages the flow of electric current. Now that you have an inkling, let us delve deep and understand the categories of semiconductors:
Memory chips: Serve as temporary storehouses of data and pass information to and from the computer’s inner core.
Microprocessors: Central Processing Units that contain the logic to perform tasks (for example ‘Intel Inside,’ refers to a semiconductor within the computer).
Commodity Integrated Circuit: These are “standard chips” and are used in routine processing.
System on a Chip (SOC): An integrated circuit chip with an entire system’s capability housed in it, for higher levels of miniaturization and power efficiency.
The global pecking order
Here’s a ranking from AzoNano, an online publication for the Nanotechnology community:
Taiwan produces approximately 50% of the world’s semiconductors, while South Korea is home to a vast network of over 20,000 semiconductor-related companies.
Despite possessing only 12% of the global manufacturing capacity, U.S. semiconductor manufacturing companies hold 40% of the global IC design market share.
The U.S. leads in providing crucial design automation software and core intellectual property (IP) for chip development. U.S. companies also own and operate the largest wafer fabrication plants, and supply 44% of the global wafer fab equipment.
Japan, ranked third behind South Korea and Taiwan in the semiconductor manufacturing supply chain, accounts for more than 50% of the semiconductor material production market, and around 30% of the equipment-production market. China has made significant strides in catching up but continues to rely on foreign suppliers for its most advanced semiconductor needs.
However, flip the discussion towards rare earths, the key input for semiconductors, and the discovery is startling: China dominates global production of the vast majority of the 17 different rare earth elements with an output of 240,000 metric tons in 2023, followed by USA, Myanmar, Australia and Thailand. Our country ranks 6th, with rare earths mine production of 2,900 metric tons.
Lagging behind in rare-earth extraction
India accounts for 0.83% of global rare earths production, China leads with 68.57%, and the United States ranks a distant second with 12.29%. If India must progress towards a greener future, and accelerate energy transition to mitigate climate change, the supply side of critical minerals such as rare earths must be stabilized and dependence on imports reduced significantly. In this context, the 2023-24 Economic Survey tabled in the Indian Parliament has identified India’s critical mineral dependence on China as a major concern.
The alternative is to focus on domestic exploration and production. According to a research paper penned by Professor Arun Vishwanathan, Head of Department of Security Studies, and doctoral scholar Ankit Kumar, Central University of Gujarat, despite the increased focus on critical mineral exploration, the government is unable to find takers for most of the mineral blocks it is offering for exploration. Since November 2023 the Ministry of Mines has carried out four rounds of auctions totalling 49 critical mineral blocks. But most of the mineral blocks have remained unsold due to insufficient number of bids, the researchers say.
Vishwanathan and Kumar attribute the lack of response from the domestic mining industry primarily to the unavailability of extraction and processing technologies within India, which again turns the focus on skill development and technology upgradation which will help reduce dependence on imports from China.
Thirst for water
According to the World Economic Forum, the semiconductor manufacturing process calls for use of ultrapure water to rinse residue from silicon chips during fabrication. Ultrapure water, which is thousands of times cleaner than drinking water, is treated through processes such as deionization and reverse osmosis to remove pollutants, minerals and other impurities that can damage chips. The downside is it takes around 1,400 to 1,600 gallons of municipal water to make 1,000 gallons of water. An average chip manufacturing facility today can use 10 million gallons of ultrapure water per day.
Overview through, some understanding gained, now let’s hear from the experts on talent shortage and talent creation:
Creating a training ground for semiconductors
“The scale, size and power rating of the chips can vary from low to high current. Materials inside the chips – titanium, gold, aluminum, copper or gold – are used in such minuscule quantity they can be seen only in a microscope,” says Srikanth N Seelin, President, Metlink Associates, San Francisco, who has been involved in semiconductor testing and production for over 30 years. He points out that just as a low-power imaging chip in a mobile phone camera gives the user power to zoom, the high-frequency semiconductor chipset in a satellite system enables real-time audio and video calls across two continents.
When asked about India’s current dependency on import of chips, Mr. Seelin cautions that the shortage is not just about materials that we require to manufacture a semiconductor. “It is a little bit more complex. Rare earths is only a start point, we also need composite electronic materials, chemicals and gases.
“Safety protocols must be in place for cylinder pressure, mixtures, piping and labeling. In addition, sustained critical super-purified (de-ionized) water supply, along with high degree surge-protected 24 x 7 power supply and hi-precision overload protection units across the spectrum of chip manufacturing equipment are among fundamentally necessary features,” Mr. Seelin said. “This brings us back to the need for training of personnel by trainers with excellent domain knowledge and experience.”
A tremendous opportunity exists in India for skilling, upskilling and reskilling, says Vinod Keni, a Bengaluru-based VC with a track record of investments in emerging technologies who is partnering with Mr. Seelin to launch talent training in India.. “Companies, domestic and foreign, can express satisfaction with infrastructure available in India, and will appreciate the Production Linked Incentive schemes being rolled out by state governments. All this will succeed only when we have trained manpower for the semiconductor industry.”
Towards bridging the talent gap, Mr. Seelin and Mr. Keni, who hail from Karnataka, are in discussion with the State government to create customized training programs. “The support that is being extended by Karnataka State, I believe will be extended by other governments as well, because locally available trained talent will encourage investors to select a specific State.
“Hence, I am sure States will start working with people like us, to launch academies for semiconductor training. Trainers will have to remember they are part of a rapidly transforming vertical and therefore must work closely with corporates, academia and research institutions to ensure the training curriculum is in line with evolving industry needs,” Mr. Keni said.
As for resource availability, one report estimates that India currently accounts for 20% of global semiconductor design talent. The central government has introduced the Chips to Startup (C2S) programme, aimed to train 85,000 engineers qualified in Electronic System Design and Manufacturing (ESDM) over five years. Even more encouraging is the government’s setting up of ‘India Semiconductor Mission’ and its commitment of Rs. 2,30,000 crores to position India as a global hub for electronics manufacturing with semiconductors as the foundational building block.
T.R. Shaswath, CEO and Co-Founder of Mindgrove, an enterprise engaged in design of SoCs for consumer electronics, automotive and defence applications, believes India is on the road to prominence in semiconductors. “As a company, we are ‘fabless,’ which means we focus on innovative chip design while outsourcing fabrication and manufacturing.” As for building skillsets, the basic skills for semiconductor design are identical to electronics and software talent requirements, Mr. Shashwath said.
As for sourcing, his company targets Tier 2 colleges for fresher recruitment. “We use a mixture of in-house training and work-integrated learning programmes offered by institutes such as IIT Madras and BITS to upskill our team and get them ready for the real world. Semiconductor design can only be learnt by doing, and we try to give our team real problems to solve very early,” he said.
A shift to productizing technology
Our erstwhile and current strength in Information Technology is also a chink in our armour, when it comes to semiconductors. Traditionally, Indian companies have excelled in IT services, and Product has always come second. Only in recent times, SaaS enterprises originating from India have productized martech as a (cloud) service.
To emerge as a nation with tangible products, to keep pace or to stay ahead of the global race for semiconductors, India must work on the following, according to Mr. Shaswath: International certifications are essential to be able to access lucrative overseas markets. Currently, Indian companies must reach out to international agencies for product certification. Empowering Indian agencies such as Standardisation Testing and Quality Certification (STQC) Directorate and encouraging private players in this area would open doors to domestic certification.
Design-Linked and Production-Linked Incentive Schemes can be enhanced with projects with a larger outlay. Seamless procedures will make the schemes even more effective. On the usage, side, India must encourage domestic Electronics Manufacturing Services manufacturers to use locally sourced chips. This could take the form of subsidies and negative import lists.
(The writer is a former journalist now serving as a communications advisor. Views expressed are his own)
Published – October 22, 2024 05:33 pm IST